An Insight into Mechanical Recycling vs Chemical Recycling
29 Jul, 20248:00As the global population grows, so will the use and demand for plastics. According to Roland...
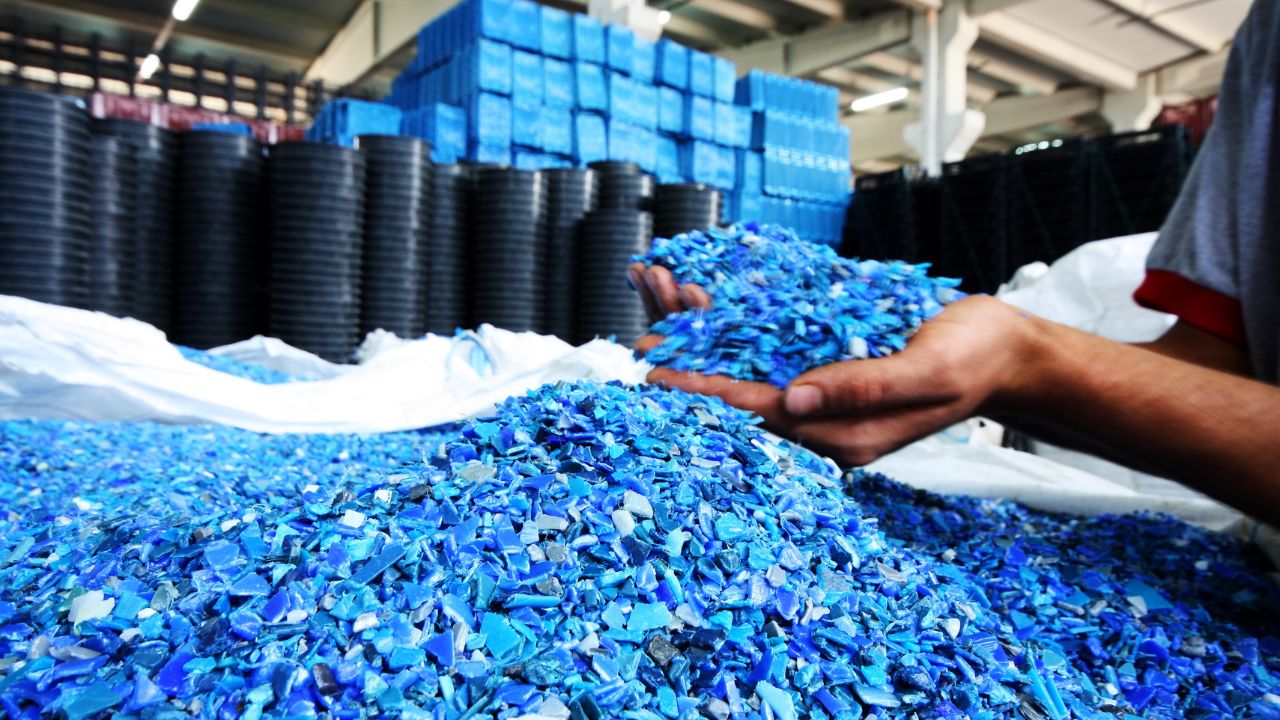
As the global population grows, so will the use and demand for plastics. According to Roland Berger, plastic waste is expected to rise from 372 megatons recorded in 2023 to 510 megatons by the middle of the century. According to McKinsey, up to $50 billion in investments may be required by 2030 to support the global scale-up of these plastic recycling efforts.
Addressing this issue will require businesses to build new facilities and find talent with the specialist skills to implement the combined approach of scaling up mechanical and chemical recycling. Many companies mentioned later in this piece have already committed to utilising these technologies to tackle the challenges surrounding plastic demand.
But first, what is mechanical and chemical recycling?
This guide will answer this question by highlighting the two key processes and benefits of recycling in the chemical sector.
This blog will explore the following:
- What is chemical recycling?
- What are the benefits of chemical recycling?
- What is mechanical recycling?
- What are the benefits of mechanical recycling?
What is Chemical Recycling?
Chemical recycling is an innovative approach to breaking down plastics at the molecular level. Also known as advanced or molecular recycling, this process harnesses various technologies, including enzymes, extreme heat, solvents and sound waves, to convert plastic feedstocks into their basic building blocks. These building blocks, such as polymers, monomers, oligomers and other hydrocarbon products, are then reintroduced into manufacturing supply chains.
As a result of chemical recycling, producing these building blocks reduces the need for fossil resources within the manufacturing space. It also helps limit the quantity of plastic waste sent to landfills, making it a sustainable process.
According to Closed Loop Partners, chemical recycling is a complex process that can be segmented into three core areas: purification, depolymerisation, and conversion.
- Purification: Involves removing impurities from plastics to recover usable materials.
- Depolymerisation: Breaks down polymers into monomers.
- Conversion: Transforms the plastic waste into secondary raw materials like pyrolysis oil or syngas through processes such as gasification and pyrolysis. These outputs can be reused in a range of industrial processes.
The European Commission has circularity goals regarding plastics. By 2025, they aim to ensure that 50% of plastic packaging is recycled, with an objective of 55% by 2030. While chemical recycling is still in its relative infancy, over the coming decades, it has the potential to play a significant part in driving sustainable solutions for hard-to-recycle plastics.
As reported by S&P Global, many petrochemical companies have made commitments to recycling plastics. BASF has committed to process 250,000 metric tons (MT) of recycled feedstock per year from 2025 onwards. Braskem stated they will recycle products equating to 300,000 MT per year by 2025 and 1 million MT per year by 2030.
Dow and Shell have stated they will roll out their recycled capacity of 1 million MT per year respectively by 2025. Lyondell Basell has also said they will produce and market 2 million MT per year of recycled and renewable-based polymers by 2030.
Global energy company Exxon is also expanding its recycling facilities in the US. Their manufacturing complex in Baytown, Texas, has the capacity to meet the demand for sustainable materials by processing over 80 million pounds of plastic waste annually. By 2026, they plan to increase their capacity to recycle 1 billion pounds of plastic.
Chemical recycling investment is estimated to reach $50 billion by 2030. Much of this investment to expand the solution's capacity is forecasted to occur in Asia Pacific, North America, and Europe. As for the latter, Europe's investment in chemical recycling is projected to increase from €2.6 billion in 2025 to €8 billion by 2030. This investment is expected to increase the recycling of plastics from 0.9 Mt (metric ton) in 2025 to 2.8 Mt in 2030.
Despite being an effective solution, chemical recycling has yet to reach a stage where it can be solely relied upon to combat plastic wastage. It must work in conjunction with another solution, which is mechanical recycling.
Later in this piece, we’ll highlight what mechanical recycling is and its benefits. First, let’s outline the core benefits of chemical recycling.
What are the Benefits of Chemical Recycling?
Chemical recycling has several benefits that make it a valuable solution for companies managing plastic waste within the chemical sector. Here are the primary benefits:
- Processes Broader Plastic Waste
Chemical recycling is more versatile than mechanical recycling because it can handle a broader range of plastic waste. For example, if a type of plastic is contaminated with toxic chemicals, it may not be suitable for the mechanical process but can be recycled with the chemical recycling approach.
- Reduces Plastic Pollution
A significant benefit of chemical recycling is its ability to lower CO2 emissions and dependence on fossil fuels. The chemical process repurposes various plastics, reducing the need for new plastic production, which is a process heavily reliant on fossil fuels. Due to its ability to handle a broad range of plastics, chemical recycling also reduces the amount of plastics at landfills and waterways, which are detrimental to the environment.
Learn more about sustainability in the chemical sector by reading our blog about How Chemical Companies are Embracing Sustainability.
- Repeated Upcycling
The chemical recycling process can be repeated without degrading the quality of the plastic. This differs from mechanical recycling, which can weaken plastics over time. It can also deliver upcycling, meaning the plastic's quality is improved as it goes through the process, matching the quality of newly manufactured plastic. This purity ensures that the repurposed plastic performs close to the original plastic, making it ideal for various manufacturing purposes.
- Benefits to Businesses
By adopting chemical recycling, companies can produce high-quality products with various types of recycled plastics rather than relying on importing new materials, which incurs environmentally damaging costs. If brands demonstrate their commitment to sustainable practices such as recycling, they will attract more clients who want to partner with them and talent who want to join their business.
If you’re searching for the latest chemical jobs, read our blog on the Global Chemical Engineering Skills Gap.
What is Mechanical Recycling?
Mechanical recycling is a core part of the circular economy and the more traditional method of repurposing plastic. Many companies operating across the entire value chain of the chemical industry rely on this approach.
The process best suits the recycling of widely collected and processed plastics such as polypropylene (PP), polyethylene terephthalate (PET), and high-density polyethylene (HDPE). Mechanical recycling involves collecting, sorting, cleaning and mechanically processing plastics to create secondary raw materials without altering the chemical structure of the polymers. These raw materials can be repurposed to manufacture new products.
The mechanical recycling process involves the following stages:
- Collection and Sorting: Plastic waste at the end of its life is collected from various sources and sent to a Materials Recovery Facility (MRF). From here, the plastics are sorted by colour and other unique properties. The sorting stage is vital because different plastics have various melting points and properties.
- Shredding: Once sorted, the plastics are shredded into small pieces, making them more straightforward to process later.
- Cleaning: The sorted and shredded plastics are thoroughly washed to remove any dust, dirt, food residue, labels, and other contaminants. This is an essential step for ensuring the recycled material is moved onto other stages within the process in the best quality possible. Ultimately, at this stage, the quality of the plastics will correspond to the quality of the final product.
- Melt Processing: Also known as extrusion, the next phase of the process involves melting the shredded plastics and extruding them to form new plastic products and raw materials. At this stage, additional steps like filtration may be used to ensure the new plastic is free of impurities. Here, the newly formed plastic can be repurposed for various products, from automotive parts to packaging.
According to AMI, China topped the leaderboard for recycling the highest volume of global plastic waste in 2023. Despite recycling the most plastic waste, Europe and North Asia have more developed systems. Mechanical recycling is the preferred method globally, accounting for over 99% of European recycled materials.
Mechanical recycling output is expected to reach nearly 55 million tonnes by 2030, over 50% greater than recorded in 2022. With this growth, the industry has significant opportunities, reflected by the recycling of commodity plastics such as polyethylene (PE), which is only expected to reach 16.5% by 2030. Dow CEO Jim Fitterling has said mechanical recycling has the potential to meet 15% of PE demand worldwide by 2050.
What are the Benefits of Mechanical Recycling?
Mechanical recycling also delivers numerous benefits to the chemical space. Here are the top benefits associated with this traditional approach to recycling:
- Trusted Traditional Process
Mechanical recycling dates back to the 1970s and has a long-standing history of reliability. Its established presence within the industry makes it a widely accepted and accessible process for repurposing plastics.
- Reduces Plastic Waste
Mechanical recycling, like chemical recycling, plays a crucial role in reducing plastic waste. By converting plastic waste into new products and raw materials, mechanical recycling eliminates the need to send plastic waste to landfills or incinerators, supporting global environmental and sustainability efforts.
- Economic Growth
With its trusted and reliable process, the mechanical recycling industry has the potential to contribute to economic growth. As chemical recycling cannot be solely relied upon, mechanical recycling will continue to be needed to transform waste into valuable resources. This approach will continue fueling a circular economy, creating employment opportunities throughout the mechanical recycling process.
- Increased Savings
Mechanical recycling requires less energy than processes used for new plastic resins and is ultimately an energy-efficient solution. It is also regarded as a typically cheaper recycling solution due to its established and accessible processes and facilities. The mechanical approach is an attractive option for manufacturers focused on cutting costs and carbon footprints.
Discover more about the chemical industry by reading our blog on the 5 Biggest Chemical Exporters In The World.
Final Thoughts on Mechanical vs Chemical Recycling
As the global demand for plastics rises, the importance of effective recycling methods cannot be overstated. Mechanical and chemical recycling each offer unique benefits that are essential for tackling the growing plastic waste crisis.
Mechanical recycling, with its established infrastructure and cost-effectiveness, plays a pivotal part in reducing plastic waste and conserving resources. At the same time, chemical recycling provides a versatile solution for processing hard-to-recycle plastics and upcycling materials, offering an approach that can support mechanical methods.
Together, these two recycling processes are essential in driving the circular economy, reducing the environmental impact of plastic waste, and supporting sustainable growth in the chemical sector. By scaling up both recycling methods, the world can make great progress towards a more sustainable future.
We Specialise in Chemical Recruitment
If you're searching for talent to grow your business in the mechanical or chemical recycling space, NES Fircroft's contract and permanent hiring services can help. Alternatively, if you're a candidate looking to register for chemical jobs, we are best placed to support your career aspirations.
We are specialists in the chemical recruitment space and have access to an extensive global talent and client network. Regardless of your recruitment challenges, whether you're a fast-growing business or an ambitious candidate, we can connect you to the top people and opportunities available.
Contact NES Fircroft today to see how we can support you with your chemical recruitment needs.