Is Your Mining Project Delayed? Here’s How a Flexible Workforce Can Get Your Project Back on Track
09 Apr, 202514:18Delays and cost overruns have become commonplace in the mining industry. A combination of ge...
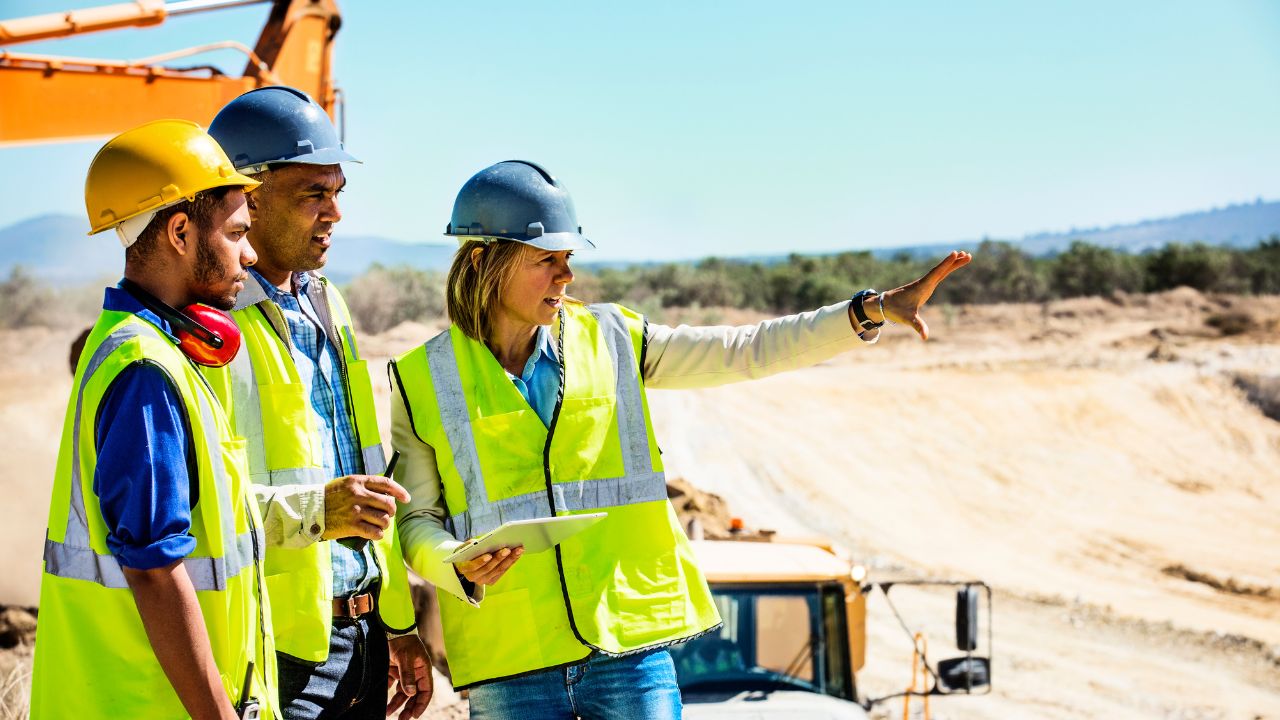
Delays and cost overruns have become commonplace in the mining industry. A combination of geopolitical factors, regulatory issues, supply chain disruptions, and inflation exacerbates the challenges of meeting surges in demand.
Outdated systems, inefficient processes, staff shortages, and slow recruitment times complicate these challenges. Multiple issues affecting a project simultaneously can lead to significant and long-lasting problems, potentially risking project cancellation.
According to a 2017 study by McKinsey, 80% of mining projects are delayed and usually exceed their budgets by 43%. EY analysed 192 global mining and metals projects with budgets over $1 billion and found that 64% faced budget or schedule overruns.
Some of these causes are, to a degree, beyond a company’s control, but circumstances within a company often worsen the effects of delays. Resolving these additional stumbling blocks can significantly improve a mining company’s chances of getting a project back on track.
Many delays can be addressed through effective staffing contingency planning, utilising temporary contractors, and leveraging skilled professionals to identify and tackle the underlying causes of delays. This article explores strategies mining companies can implement to attract talent and expedite project timelines while minimising recurring issues.
Leading Causes of Delays in Mining Projects
Delays in mining projects often result from a combination of factors rather than a single cause. When these issues aren’t accounted for in risk assessments and proper planning, they can lead to increased costs and a domino effect of further delays.
Inadequate infrastructure
Delays often stem from ineffective infrastructure and systems. Outdated processes for risk management, contractor oversight, and payroll are usually buried in inefficient systems, leading to errors and knowledge gaps due to staff turnover. Without a unified digital strategy, data collection and reporting become cumbersome, with disparate systems creating further administrative burdens.
Additionally, non-centralised and outdated data systems, reliance on manual spreadsheets, and unsuitable file formats exacerbate delays. A recent study found that nearly 90% of mining companies facing project delays were using manual tracking methods, which are time-consuming and error-prone.
Without tailored digital solutions to centralise information, communication suffers, leading to frustrations among management, contractors, and suppliers. Early project management issues can significantly impact a project’s lifecycle, causing budget overspending and reducing productivity and profitability.
Managing stakeholder expectations
The economic benefits of mining often conflict with local negative perceptions, especially when projects lack proactive communication with stakeholders. Environmental and social issues can lead to public opposition and reputational damage if not addressed.
Mining companies face challenges from local communities, environmental groups, and Indigenous peoples, with social media amplifying these concerns. Failing to engage effectively can result in project delays, legal disputes, or cancellations. Strong community engagement and transparent communication are essential to mitigate resistance.
Supply chain issues
The mining industry faces a complex supply chain driven by global energy shortages, raw material scarcities, and high shipping costs intensified by inflation. Increased demand for shipping containers further elevates transportation prices. Investors require timely project completions with robust risk management, often expecting a 20% buffer for cost overruns.
Current supply chain challenges have led to a tough pricing environment, with suppliers hesitant to absorb market fluctuations. High demand results in production constraints, and some suppliers now seek to rebalance risk, refusing to participate due to high demand or imposing strict payment and pricing conditions. Mining companies lacking a solid supply chain plan struggle to secure investment and trustworthy suppliers, risking significant delays or project shutdowns.
Economic and geopolitical factors
Demand significantly contributes to delays in the mining industry, as projects often hinge on long-term price projections. Unexpected drops in commodity prices can render projects unviable, necessitating effective risk management strategies. While some demand changes are predictable, geopolitical shifts can also impact project viability.
For instance, new governments may alter climate policies, and regulatory changes are usually communicated in advance. However, unforeseen geopolitical issues—like disruptions in logistics or changes in demand due to conflicts—pose serious challenges for companies reliant on specific project plans.
Disruption in the workforce
Over time, businesses will experience team shrinkage due to retirements and talent leaving for better opportunities. The global skills market can also lead experienced workers to relocate for more lucrative positions. Consequently, mining companies may struggle to find permanent replacements, resulting in skills gaps that can impact operations.
Poor contractor and staff management, including inadequate training, ineffective team management, payroll delays, and lack of communication, can deepen retention issues. Companies employing a mix of local and foreign workers face additional regulatory and tax challenges, and employees who feel poorly managed are likely to seek opportunities elsewhere.
How a Flexible Workforce Can Help
The mining sector's greatest asset is its people, and finding solutions to delays requires skilled and experienced workers. However, the need for these skills is often temporary, making it challenging to attract permanent staff. A practical solution is to utilise temporary contractors.
Contract workers seek national or global opportunities, gaining diverse experiences and skills while aligning their careers with their lifestyles. They contribute by increasing output, implementing efficiencies and cost reductions, and training permanent staff.
Addressing skills gaps
The mining sector often faces a shortage of experienced professionals due to retirements and competition from other industries. Contract workers can bridge these gaps by offering specialised skills in areas like geological analysis and mine planning. This approach enables mining companies to tackle complex projects and adopt new technologies without the long-term commitment of permanent hires. Additionally, contractors can train existing staff and improve efficiency, especially when updating legacy systems.
Increasing workforce flexibility
On-hire labour agreements provide mining companies with significant benefits in flexibility and scalability. They enable quick adjustments to the workforce in response to changing project demands, which is crucial for recovering delayed projects. Temporary workers can be beneficial when additional budget is needed for a short period, such as 6 months, to restore production levels.
Managing peak workloads
Contract staff can supplement the existing workforce when urgent tasks or tight deadlines arise, helping mining companies maintain productivity without overburdening permanent employees. Increased workloads often occur due to rising demand or project beginnings. Temporary contractors support permanent staff, reducing risk and allowing core teams to focus on critical areas.
Cost-effective staffing
Using temporary workers through on-hire labour agreements can be more cost-effective than hiring permanent staff. It reduces long-term salaries, benefits, and training expenses, especially when addressing project delays where candidates often seek permanent roles.
Contract staffing partners, like Managed Service Providers (MSP), can manage contingent workers' hiring, payroll, training, and administrative tasks, allowing businesses to focus on core activities and recovery efforts. Temporary workers help minimise downtime, ensuring skilled professionals are available to mitigate project delays.
How to Implement a Temporary Workforce
Onboarding and training
Effective onboarding and training are essential for integrating temporary workers into projects. A customised onboarding process should include comprehensive documentation on company policies, culture, and tasks and guidance on necessary tools and resources.
Prior training and experience are crucial for mining engineers, particularly site-specific health and safety training. When hiring internationally, it’s important to consider laws regarding expatriate staff, including tax requirements and immigration laws, and to seek advice on any related costs.
Mining companies that provide straightforward onboarding, training paths, and an understanding of legal obligations can reduce delays in deploying temporary workers.
Safety considerations
Mining is a hazardous job, subject to strict safety regulations to protect workers' physical and mental health. While laws differ by country, ensuring safety and well-being is a top priority for all mining companies. Each company must have specific workplace practices and requirements. Including audited training during onboarding is essential, especially for temporary contractors unfamiliar with site hazards. Companies must also ensure contractors possess the necessary qualifications, certifications, and permits. By providing adequate training and a clear understanding of project risks, mining companies can reduce the likelihood of accidents involving temporary workers.
Team integration
Clear communication is vital for integrating temporary workers. It's important to discuss with existing staff the reasons for hiring temporary employees and to assure them that their jobs are secure. Introducing contractors to their teams and organising team-building activities can foster bonds, creating a sense of unity among all staff.
This is especially crucial for expatriate contractors in mining projects who may face language or cultural barriers. Effective integration allows temporary and permanent staff to collaborate seamlessly, ensuring safety and efficient training. Moreover, it facilitates skill transfer, enabling contractors to expand their expertise while helping to prevent future delays.
Performance management
Implementing an effective performance management system is essential for the success of temporary workers in the mining industry. This system should align employee goals with the organisation's strategic plan and support business objectives. Regular goal-setting and feedback are crucial from day one until departure.
Real-time feedback and support help temporary workers evaluate their performance holistically. To recover from project delays, mining companies must ensure that temporary workers are efficient and issues are addressed swiftly, enhancing overall effectiveness and ROI.
Engage with a Specialised Staffing Provider for Mining Engineering Professionals
Mining companies often struggle to balance daily operations and manage increased workloads from production delays, which can stretch existing teams thin. Specialist recruitment firms focused on mining can help by providing qualified candidates quickly, thanks to their regional expertise and candidate databases.
For a more comprehensive solution, companies can turn to MSPs, which handle hiring, background checks, payroll, and benefits management for temporary contractors. This alleviates the hiring burden, allowing mining companies to focus on effectively integrating contractors and minimising delays.
Long-Term Workforce Strategy
Mining companies need a long-term workforce strategy to utilise temporary workers, aligning workforce planning with mine effectively plans to last 10 to 20 years. Regularly updating talent strategies is essential, enabling companies to anticipate future skill needs and assess their employee value proposition against competitors.
There are three main approaches to developing a temporary workforce strategy: in-house, outsourcing, or a hybrid model.
In-house provides direct control but can be costly and slow to implement since permanent staff must be maintained.
Outsourcing offers a quick solution through specialised staffing partners. While they can effectively identify and resolve delays, costs may vary and aren't always the most economical.
Hybrid models combine internal hiring specialists with external recruiters, allowing for budget management and flexibility. However, it carries the risks of both in-house and outsourcing methods.
Ultimately, a strong strategy should;
- Forecast future needs using project requirements, data analytics, workforce assessment, project risks, and business areas vulnerable to external causes of delays, such as suppliers, machinery, and logistics.
- Engage with internal and external stakeholders to identify the delays, their causes, and long-term effects.
- Identify the areas where skills gaps cause delays and implement training plans to fill these gaps.
- audit internal processes, systems and applications, supplier lists, and business practices that could be causing or extending delays.
- Implement plans to ensure key knowledge is transferred from existing employees before they leave.
- Implement a temporary workforce hiring strategy with realistic timelines and budget requirements.
- Focus on critical hiring and placing mining engineers where needed most.
- Utilise specialist recruitment staffing partners to source and place temporary workers quickly and efficiently.
- Use KPIs, workforce feedback and data analytics to track the effectiveness of the temporary workforce strategy.
- Ensure temporary workers and contractors can effectively train teams to upskill the permanent workforce and mitigate the effects of future delays.
Partner with a Global Mining Recruitment Agency
The mining industry's reliance on temporary workers enhances project recovery and operational efficiency. By utilising skilled professionals to tackle specific challenges, companies can bridge skills gaps, manage peak workloads, and increase flexibility. This strategy aids in getting delayed projects back on track and enables quick adaptation to market changes.
While mining companies may face budget strains due to delays, investing in a temporary workforce can lead to significant savings in the medium to long term. It reassures investors that companies are actively addressing financial risks associated with delays.
Additionally, implementing strategies that protect workers and minimise environmental damage fosters trust among local stakeholders. If your mining operation is facing costly delays, NES Fircroft can assist. With global offices and specialised mining teams, we offer tailored advice to help you find the right talent and get your project back on track.
Our recruitment team possesses expertise in both white-collar and blue-collar sectors and in permanent and labour-hire placements. This ensures that we can effectively assist you in locating the skilled mining engineers required for your operations. We’re your ideal mining recruitment partner. Contact us today to swiftly address your workforce challenges.